Low Cement Refractory Castable and Superfine Powder Technology
- Rongsheng
- Aug 27, 2020
- 2 min read
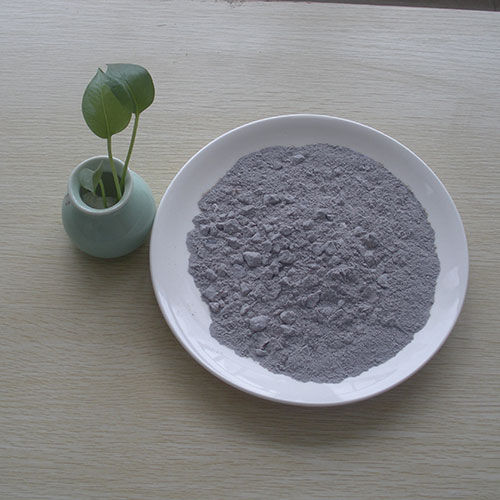
Low cement series refractory castables are developed based on the clay combined refractory castable system. It has high density, low porosity, high strength, low wear, thermal shock resistance and good corrosion resistance.
Although aggregates and powders in traditional aluminate cement refractory castables have high bulk density and compactness, they use a lot of water during the construction process, and many pores are filled with water. After the water evaporates, the pores reappear and the strength changes. low. In the low-cement refractory castables, the cement content is less than 8% and the construction water consumption is less than 7%. In addition, the ultrafine powder in the low-cement refractory castables will fill the gaps in the structure during use, making the structure more dense and the porosity Will be reduced accordingly, so a series of properties such as strength and wear resistance are better than traditional aluminate cement refractory castables.
The production methods of ultrafine powder are divided into two categories: mechanical crushing method and chemical preparation method. The former has simple production process, large output, no agglomeration of micro powder and low cost; the latter has high purity, small particles and easy control of its shape and particle size distribution, but high cost and easy agglomeration. Among the unshaped refractory materials, the more widely used varieties of ultrafine powder technology include: active SiO2 powder and α-Al2O3 powder, followed by SiC powder, high alumina powder, white corundum powder, zircon powder and spinel powder.
Generally speaking, the smaller the particle size of the ultrafine powder, the greater the improvement in the performance of the refractory castable, but the cost will also increase. In the actual use of superfine powder, the powder not larger than 5μm accounts for 40%-80%.
Comments