Low-creep High-Alumina Bricks Checker Bricks 19/37 Holes Special for Hot Blast Stove
- Rongsheng
- May 9, 2023
- 3 min read
High alumina checker bricks are mainly used for masonry in the middle of the regenerator of the hot blast stove. Low-creep high-alumina checker bricks with 19 holes and 37 holes are specially used for hot blast stoves. High alumina checker bricks are used in the middle of the regenerator of the hot blast stove. According to the physical and chemical indicators, the products can be divided into three grades: RL-65, RL-55, and RL-48. The brick type is usually divided into 7 holes, 19 holes, and 37 holes according to different furnace types and different heat storage areas.
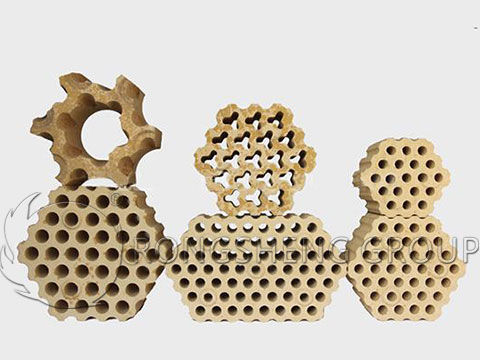
Rongsheng high alumina refractory brick manufacturer can provide regular size low creep high alumina checker bricks. Most of them are designed and customized according to the requirements of the furnace type. Hole bricks have 7 holes, 19 holes, 37 holes, 65 holes, etc., and support customization.
Product Features of Low Creep High Alumina Checker Bricks
1. Refractoriness. The refractoriness of high alumina bricks is higher than that of clay bricks and semi-silica bricks, reaching 1750~1790°C. Belongs to advanced refractory materials.
2. Load softening temperature. Because the content of Al2O3 in high aluminum products is high, the amount of impurities is small, and the formation of fusible glass is less. Therefore, the load softening temperature is higher than that of clay bricks. However, because mullite crystallization does not form a network structure, the softening temperature under load is still not as high as that of silica bricks.
3. Slag resistance. There is more Al2O3 in high alumina bricks, which are close to neutral refractory materials and can resist the erosion of acid slag and alkaline slag. Because it contains SiO2, the ability to resist alkaline slag is weaker than that of acid slag.

Low-creep high-alumina bricks for hot blast stoves Dome composite bricks Good thermal shock stability
Low-creep high-alumina composite bricks for hot blast stoves are made of calcined, selected high-alumina bauxite clinker and binders, which are first granulated and powdered. After mixing in a certain proportion, it is a product that is pressed into shape and fired at high temperature. According to physical and chemical indicators, it is divided into five grades: LZ-80, LZ-75, LZ-65, LZ-55, and LZ-48. The product has the properties of high strength, high temperature resistance, corrosion resistance, high temperature volume stability, etc., and is mainly used in high temperature parts of industrial kilns.
Features and advantages of combined bricks at the combustion port of the hot blast stove
Combustion port combination bricks of hot blast stove are resistant to high temperature, erosion, erosion and thermal shock stability. It is installed in the kiln body, and it is characterized in that it includes a refractory brick body, a combustion space and a fire injection hole, and a metal anti-radiation layer is pasted on one end of the refractory brick body. A metal anti-radiation layer is pasted on one end of the burner brick, and the anti-radiation layer can radiate the heat emitted from the furnace body back into the furnace. It also avoids the heat loss of the burner brick at high temperature and high heat. Thus, the heat utilization rate of the kiln and the thermal efficiency of heat treatment are improved, and energy is saved. There are various specifications of burner bricks, which can be applied to high-speed flame-injection burner bricks of various roller kilns, tunnel kilns, and shuttle kilns using light diesel oil, coal gas, natural gas, petroleum liquefied petroleum gas and other fuels.
Combustion port combination brick function of hot blast stove
1. Heat the fuel to the ignition temperature in the burner brick to make it easy to ignite and burn quickly.
2. Maintain a certain high temperature in the burner brick to stabilize the combustion process and avoid pulsation or interruption of combustion.
3. Organize the flame shape to meet the requirements of the heating process.
4. Further mixing of fuel and air.
Low-creep high-alumina bricks for hot blast stoves
Low-creep high-alumina bricks use bauxite and bonded clay as the main raw materials. Add appropriate kyanite, andalusite and sillimanite to control physical and chemical indicators and particle size composition. Raw materials such as bauxite + mullite + corundum are used as technical solutions. Low-creep high-alumina bricks for hot blast stoves have the characteristics of high strength, low creep rate and high service temperature. Rongsheng high-alumina refractory brick manufacturer (https://highaluminarefractory.com/) provides high-quality low-creep high-alumina brick products, as well as perfect pre-sales and after-sales services. It is a powerful high alumina brick manufacturer.
Comments